infineon公司的iMOTION™ IMC100系列是用于變速驅動控制的高度集成電路.器件集成了永磁同步馬達(PMSM)控制所需要的硬件和軟件,能以最低系統和開發成本使得任何的馬達系統以最短時間走向市場.器件所集成的腳本引擎允許增加應用的靈活性而不用干擾馬達和PFC控制的算法. IMC101提供單個馬達控制,而IMC102除了控制馬達有增加了增強或圖騰柱功率因素修正(PFC).器件集成的運動控制引擎(MCE)是可變速度驅動的即用解決方案,控制矢量PWM具有正弦換流和集成的保護特性,通過單分流或腿分流進行電流檢測,無傳感器操作,可選擇支持所有的霍爾傳感器(模擬或數字),可選擇增強或圖騰柱PFC控制,靈活的主接口用于馬達控制指令:UART,PWM或模擬輸入信號,支持IEC/UL 60335 (Class B),有多種封裝選擇.主要用在電冰箱,家用電器,泵和風扇以及其它PMSM驅動.本文介紹了iMOTION™ IMC100系列主要特性,系統框圖和系列框圖,多種應用框圖,以及24V低壓馬達驅動參考設計REF-Vacuum-C101-2ED主要特性,電路圖,材料清單和PCB設計圖.
iMOTION™ IMC100 is a family of highly integrated ICs for the control of variable speed drives. By integrating both the required hardware and software to perform control of a permanent magnet synchronous motor (PMSM) they provide the shortest time to market for any motor system at the lowest system and development cost. The integrated script engine allows to add application flexibility without interfering with the motor and PFC control algorithm.
iMOTION™ IMC100 is a series of highly integrated ICs for the control of a Permanent Magnet Synchronous Motor (PMSM). IMC101 devices provide control of a single motor while the IMC102 devices control the motor and additionally a boost or totem pole power factor correction (PFC).
The IMC100 series is based on Infineons Motion Control Engine (MCE) and integrate all hardware and software functions required to implement a closed loop sensorless or optionally sensor based control algorithm for permanent magnet motors. IMC100 devices do not require any software programming and can be configured for a wide range of motor control inverters.
The IMC100 series takes advantage of a new hardware platform that is based on a comprehensive set of innovative analog and motor control peripherals. The high level of integration both in terms of hardware modules and software algorithms results in a minimum number of external components required for the implementation of the inverter control.
Infineons patented and field proven Motion Control Engine (MCE) implements field oriented control (FOC) using single or leg shunt current feedback and uses space vector pulse width modulation (PWM) with sinusoidal signals to achieve highest energy efficiency. In addition to the motor control algorithm it also integrates multiple configurable protection features like over- and under-voltage, over current, rotor lock etc. to protect both the power stage as well as the motor during application tuning or in case of malfunction.
The second generation of the MCE further improves the performance of the sensorless control algorithm and adds functionality like optional sensor support for applications that require accurate rotor positioning, two types of ready-to-use PFC algorithms as well as more and flexible and faster host interface options.
The IMC100 series is offered in several device and package variants for applications from single motor control to motor control plus PFC. All devices can be used in applications requiring functional safety according to IEC 60335 (Class B).
There are multiple versions of the MCE software offered by Infineon and made available for download from the Infineon web site.
By using a special secure boot loader algorithm in combination with type specific chip IDs it is assured that these MCE software versions can only be installed onto the matching hardware derivatives, i.e. IMC100 variants for which the software has been tested and released for. Infineon as well as third parties provides tools to program these software images. For details please refer to the iMOTION™ programming manual.
The MCE integrates a script engine providing additional flexibility. The script engine can make use of analog and digital IOs for reading sensors or driving signals. The respective IOs are given in the pin lists referencing the name in the script to the physical pin of the package.
iMOTION™ IMC100系列主要特性:
• Motion Control Engine (MCE) as ready-to-use solution for variable speed drives
• Field oriented control (FOC) for permanent magnet synchronous motor (PMSM)
• Space vector PWM with sinusoidal commutation and integrated protection features
• Current sensing via single or leg shunt
• Sensorless operation
• Optional support for hall sensors (analog or digital)
• Optional boost or totem pole PFC control integrated
• Flexible host interface options for motor control commands: UART, PWM or analog input signal
• Support for IEC/UL 60335 (Class B)
• Integrated scripting engine for application flexibility
• Multiple package options
iMOTION™ IMC100系列應用:
• Refrigerators
• Home appliances
• Pumps, fans
• ...any other PMSM drive
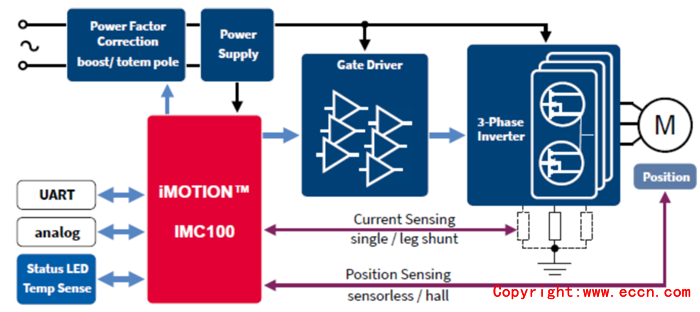
圖1. iMOTION™ IMC100系列系統框圖
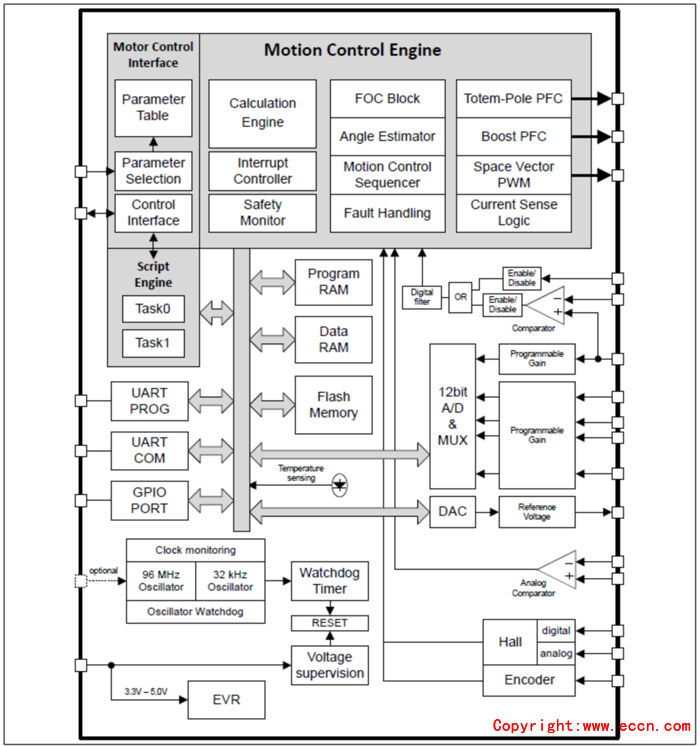
圖2. iMOTION™ IMC100系列框圖
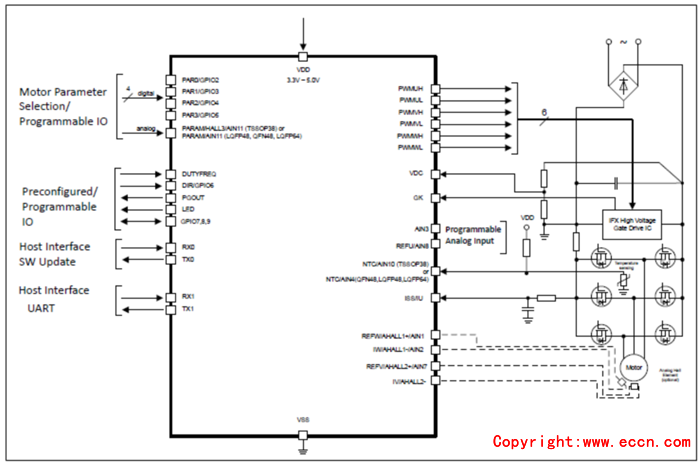
圖3. IMC101單分流配置圖
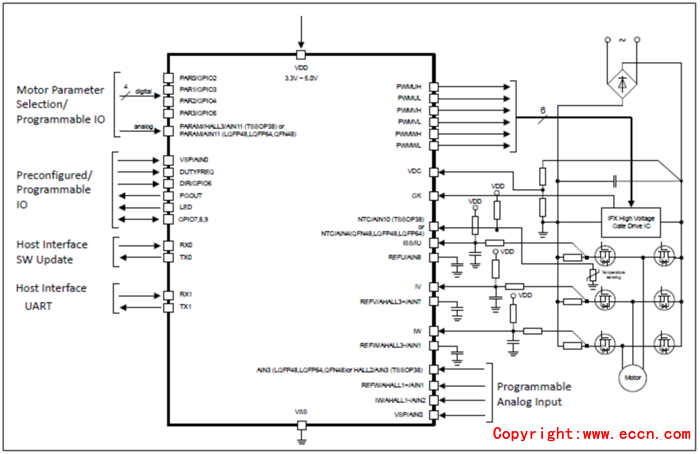
圖4. IMC101腿分流配置圖
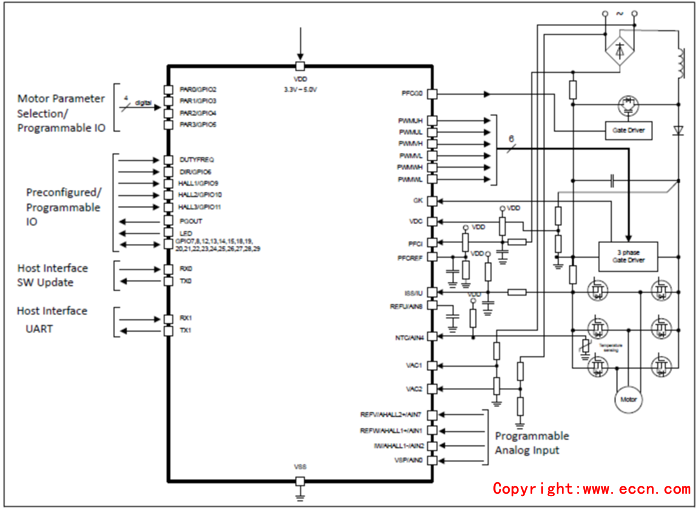
圖5. IMC102帶增強PFC控制的單分流配置圖
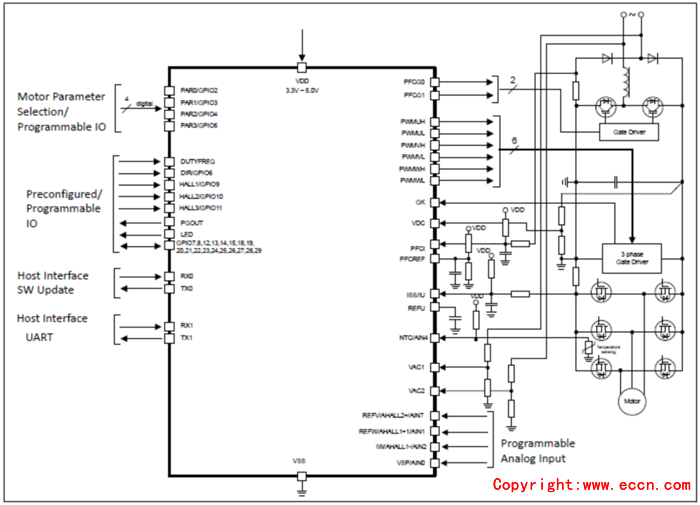
圖6. IMC102帶圖騰柱PFC控制的單分流配置圖
24V低壓馬達驅動參考設計REF-Vacuum-C101-2ED
The REF-Vacuum-C101-2ED is part of the iMOTION™ reference design kits. It is designed to provide ready-to-use, low-voltage and high-speed vacuum solutions based on Infineons thin-film SOI technology and advanced motion control engine (MCE 2.0) technology. It allows fast prototyping and fast time to market. The board is equipped with all assembly groups for sensorless field-oriented control (FOC), and reserved interface for three digital Hall sensors, so that it can be extended to other low-voltage and high-current motor applications.
The block diagram of the REF-Vacuum-C101-2ED is depicted in Figure 1, which contains iMOTION™ controller IMC101T, 3 mOhm 40 V OptiMOSTM, and 2ED2304S06F half-bridge gate driver with integrated bootstrap diode.
參考設計REF-Vacuum-C101-2ED包括:
- Gate driver IC for MOSFET
- Anti-reverse connection protection
- 12 V & 3.3 V auxiliary power supply
- VSP speed command potentiometer
- Over temperature and overcurrent protection
- Turnkey version sensor less & sensor FOC control
The REF-Vacuum-C101-2ED reference design is available through regular Infineon distribution partners as well as on Infineons website. The main features of this board are described in this document, whereas the remaining paragraphs provide information to enable the customers to copy, modify and qualify the design for production according to their own specific requirements.
An 18 V, 250 W vacuum motor is used for the default DEMO function, whose maximum speed is 100 kRPM. Please note that motor parameters need to be double-checked in MCEWizard if a different motor is used.
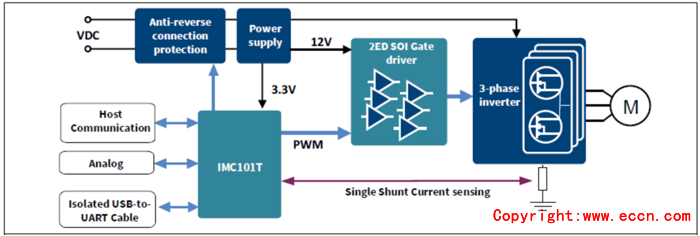
圖7. 參考設計REF-Vacuum-C101-2ED框圖
REF-Vacuum-C101-2ED is a reference design for 24 V (like 6~7S Li battery) low-voltage motor drive applications.
Main features of SOI half-bridge gate driver 2ED2304S06F include:
• Infineon thin-film SOI technology
• Fully operational to +650 V, floating channel designed for bootstrap operation
• Output source/sink current capability +0.36 A/-0.7 A
• Integrated ultra-fast, low RDS(ON) bootstrap diode
• dV/dt immune ±50 V
• Tolerant to negative transient voltage up to -100 V
• 10 ns typ., 60 ns max. propagation delay matching
• Integrated minimum dead time 75 ns, shoot-through prevention
• Gate drive supply range from 10 V to 20 V, undervoltage lockout for both channels
• 3.3 V, 5 V and 15 V input logic compatible
Main features of iMOTION™ controller IMC101T include:
· Motion control engine as ready-to-use controller solution for sensorless and Hall-sensor motor drives
· Field-oriented control (FOC) for permanent magnet synchronous motor (PMSM/BLDC)
· Optional support for Hall sensors (analog or digital)
· Space vector PWM with sinusoidal commutation and integrated protection features
· Current sensing via single shunt or leg shunt
· Integrated analog comparators for overcurrent protection
· Integrated scripting engine for application flexibility
· 3.3 V or 5.0 V supply voltage options for controller
· Flexible host interface options for speed commands: UART, SPI, PWM or analog signal
· Class B pre-certification (IEC60335) for MCE2.0 firmware
The REF-Vacuum-C101-2ED reference design characteristics include:
• Input voltage 18~30 V DC (6S ~ 7S Li battery)
• Maximum 600 W at 25 A, 24 V DC power input with on-board cooling fan
• Anti-reverse connection protection
• VSP speed command potentiometer
• 3 digital Hall interface
• User UART for script function
• Overcurrent and over temperature protection, fault diagnostic LED output
• Low-noise, single-shunt current sample
• Auxiliary power supply with 12 V, 3.3 V
• PCB is 60 mm × 115 mm (or 60 mm × 63.5 mm if cooling fan is removed), 2 layers, 1 oz. copper
• RoHS compliant
參考設計REF-Vacuum-C101-2ED主要指標:
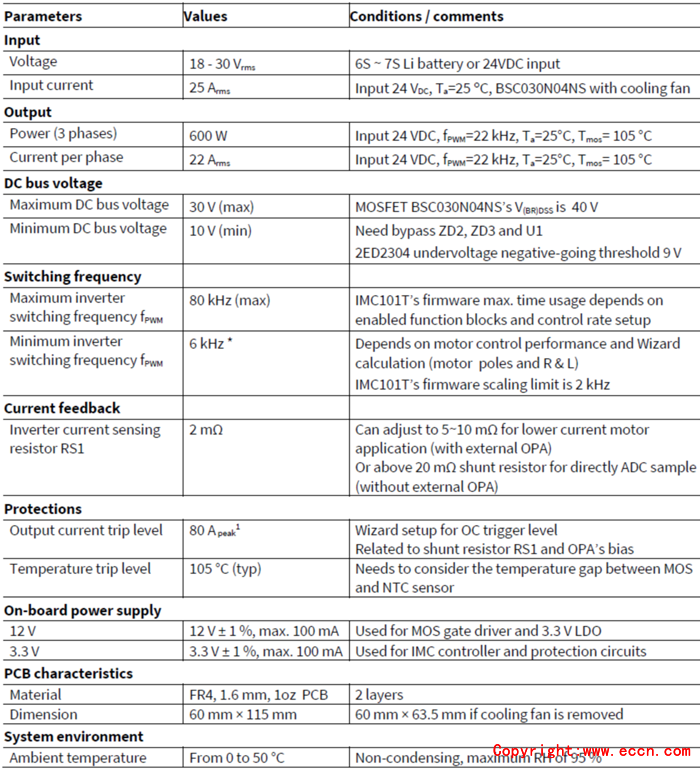
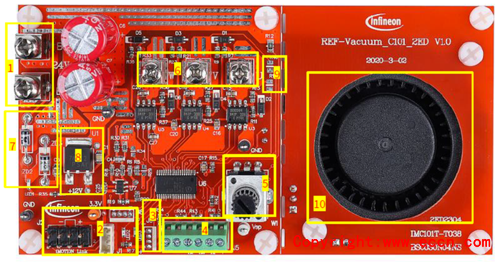
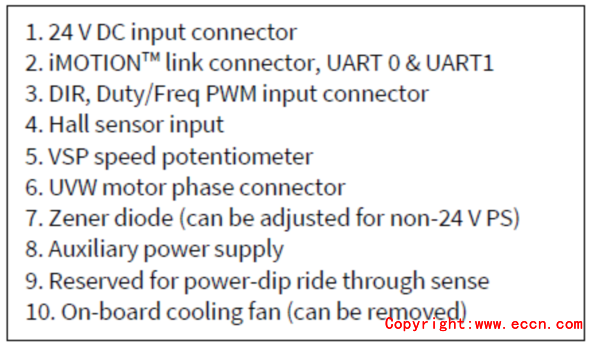
圖8. 參考設計REF-Vacuum-C101-2ED外形圖和功能分布圖(正視)
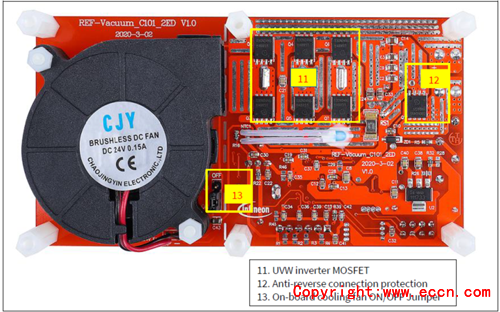
圖9. 參考設計REF-Vacuum-C101-2ED外形圖和功能分布圖(底視)
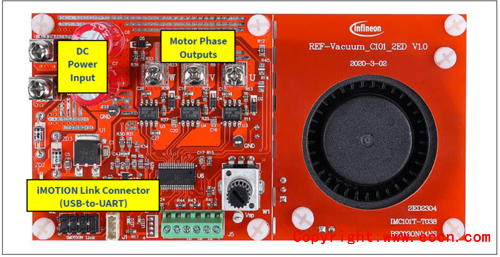
圖10. 參考設計REF-Vacuum-C101-2ED系統連接圖
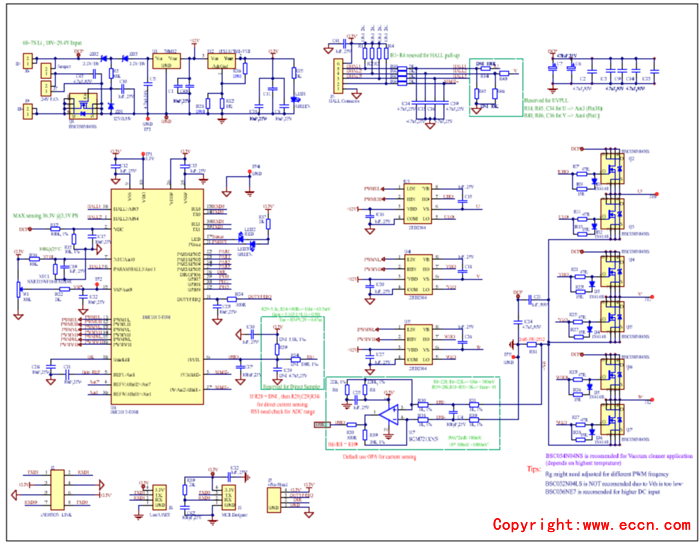
圖11. 參考設計REF-Vacuum-C101-2ED電路圖
參考設計REF-Vacuum-C101-2ED材料清單:
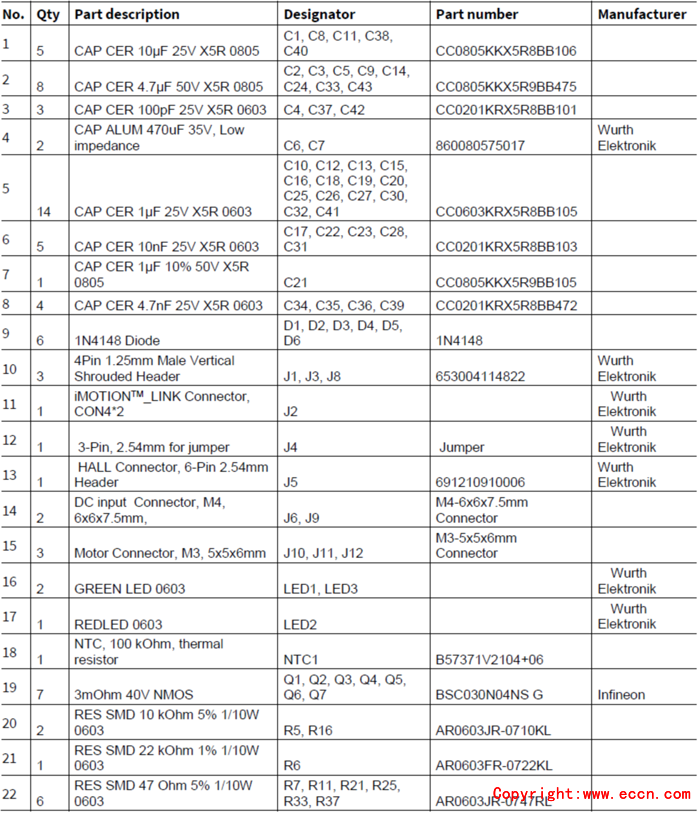
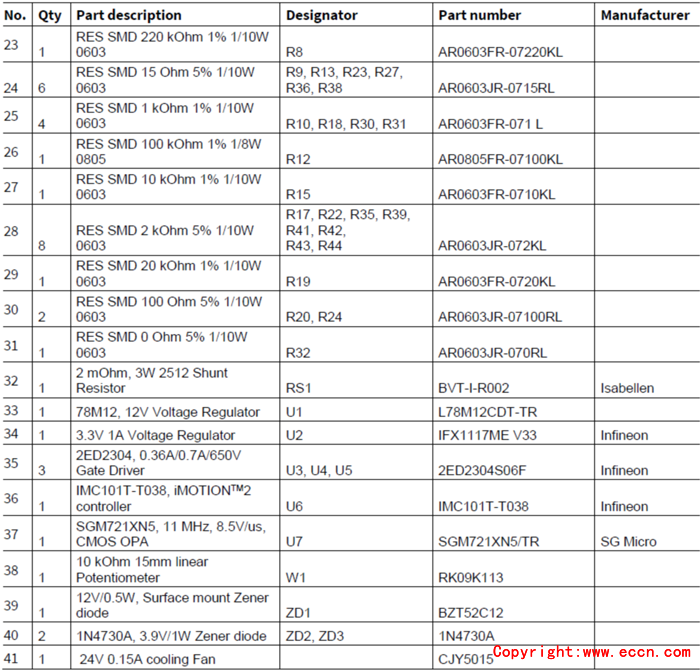
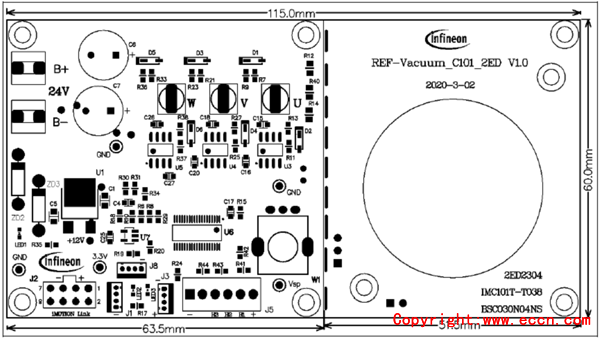
圖12. 參考設計REF-Vacuum-C101-2ED PCB裝配圖(正面)
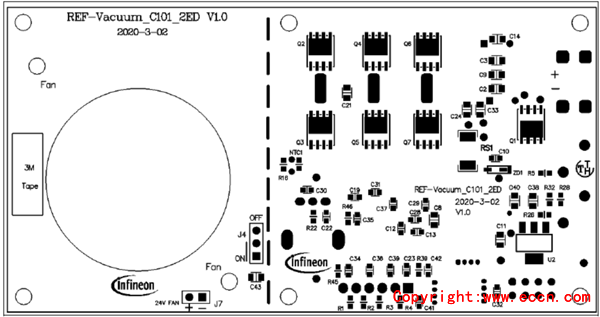
圖13. 參考設計REF-Vacuum-C101-2ED PCB裝配圖(背面)
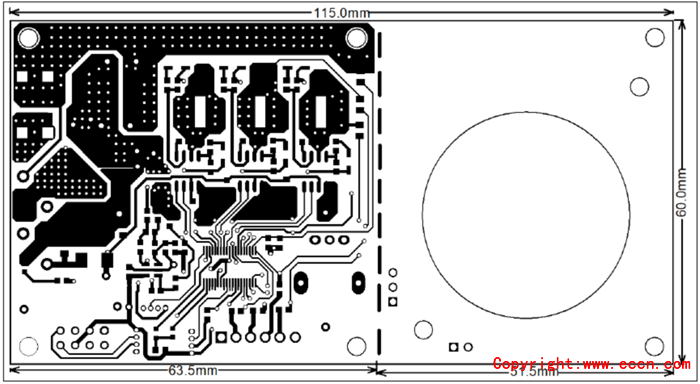
圖14. 參考設計REF-Vacuum-C101-2ED PCB走線圖(正面)
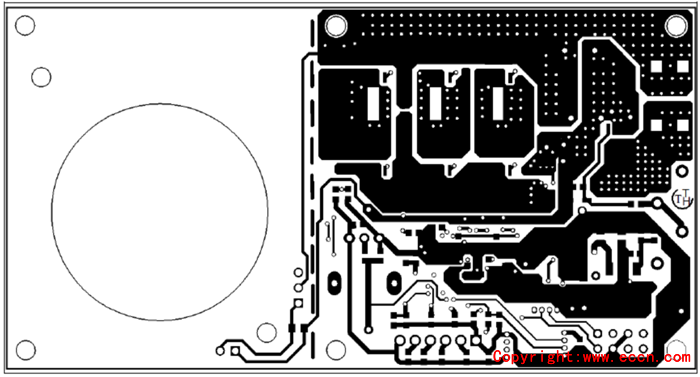
圖15. 參考設計REF-Vacuum-C101-2ED PCB走線圖(背面) |